PLAEX blocks: The Legolution in the sustainability of building materials
- Salix
- Nov 16, 2021
- 4 min read
Updated: Mar 13, 2024
Contents
What's better than building a Lego house?
Living in a Lego house made of recycled plastic!
That’s what you’ll be able to do thanks to PLAEX Bricks.
And it’s not just about homes.
The Canadian startup is upcycling plastic waste into sustainable building blocks that can be used for a wide range of structures.
Before getting into the details on the sustainability of PLAEX’s green building materials, let’s have a look at how these blocks are knocking down the barriers to sustainable construction.
A zero-waste green building innovation
When added together, building and construction sectors release about 40% of the world energy-related CO2 emissions.
According to the International Energy Agency (IEA), these should go down by 6% every year until 2030 if we want to achieve net zero carbon buildings by 2050.
Making a climate-friendly cement would help as the production of the conventional Portland type emits ca. 8% of the global carbon emissions. Just to give a sense of scale, that’s 3 times the aviation’s carbon footprint.
Not to mention waste…
According to the green building expert Keith Robertson, unused construction materials account for ca. 30% of the total rubbish ending up in landfills, with wood being second to concrete only.
The result of this?
Deforestation.
But PLAEX is coming to the rescue!
Not only are they’re turning plastic into a low-carbon cement, but their bricks interlock like Lego blocks. By connecting together the PLAEX Bricks and interlocking exterior panels, you’ll get a finished wall while cutting down on cuts (built-in pun).
Switching to this smart, modular, and environmentally sustainable building system would massively reduce the amount of waste from construction sites, thus preserving the beauty of our planet.
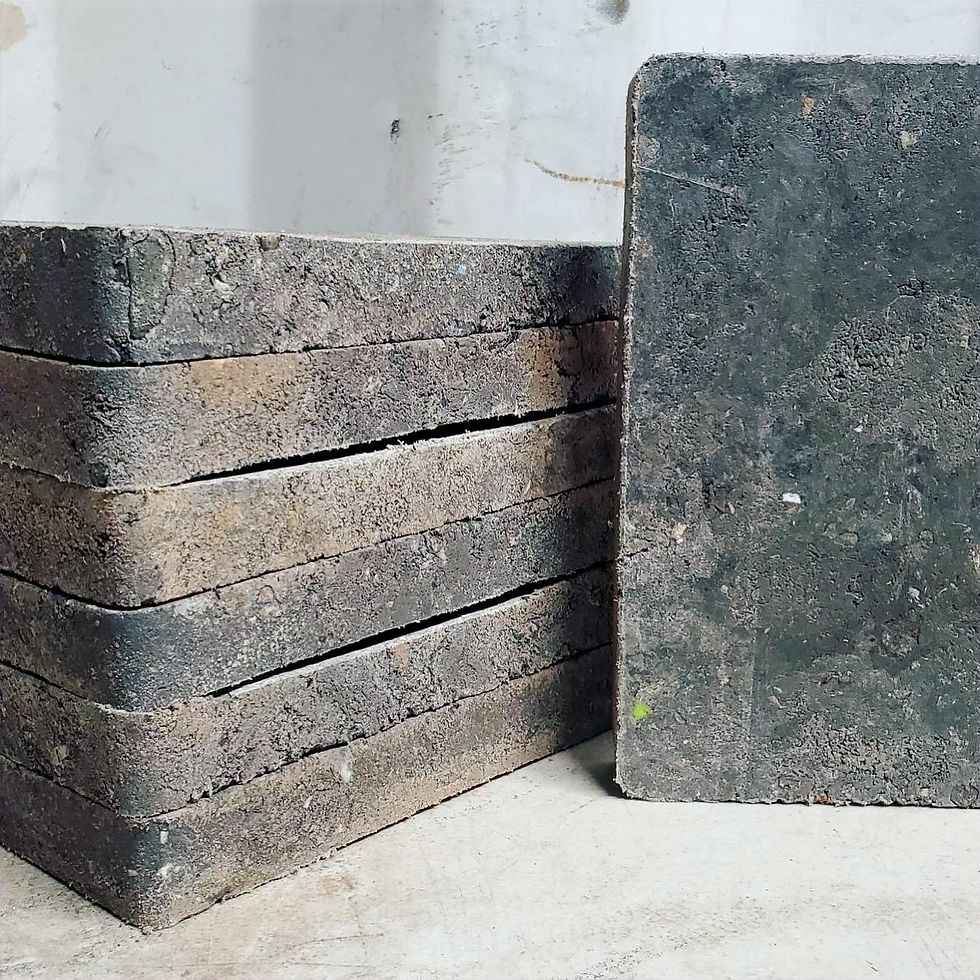
PLAEX bricks. Credits to PLAEX
A circular process for square blocks
PLAEX is also taking the plastic pressure off farmers’ shoulders. Inspired by the circular economy principles, the company claims they could convert up to 70% of agricultural plastics into materials that can be used for sustainable construction.
Ropes, silage wrap, row cover, insect netting, drip line, you name it.
Each brick will divert an approximately 10 pounds of plastic waste. When interlocking 400 of them, you’ll save as much garbage as that produced by 1 family in 1 year.
What’s even cooler is that PLAEX locks the plastic in.
Using a special coating and a high-wear exterior finish, the Canadian designers are preventing any UV degradation or chemical leaching. Because of this ingenious setup, PLAEX Bricks could last 500 years or more.
But that’s not the end of it. Even if they were to be damaged, the blocks could be reused to make new bricks.
Never-ending yet evergreen.
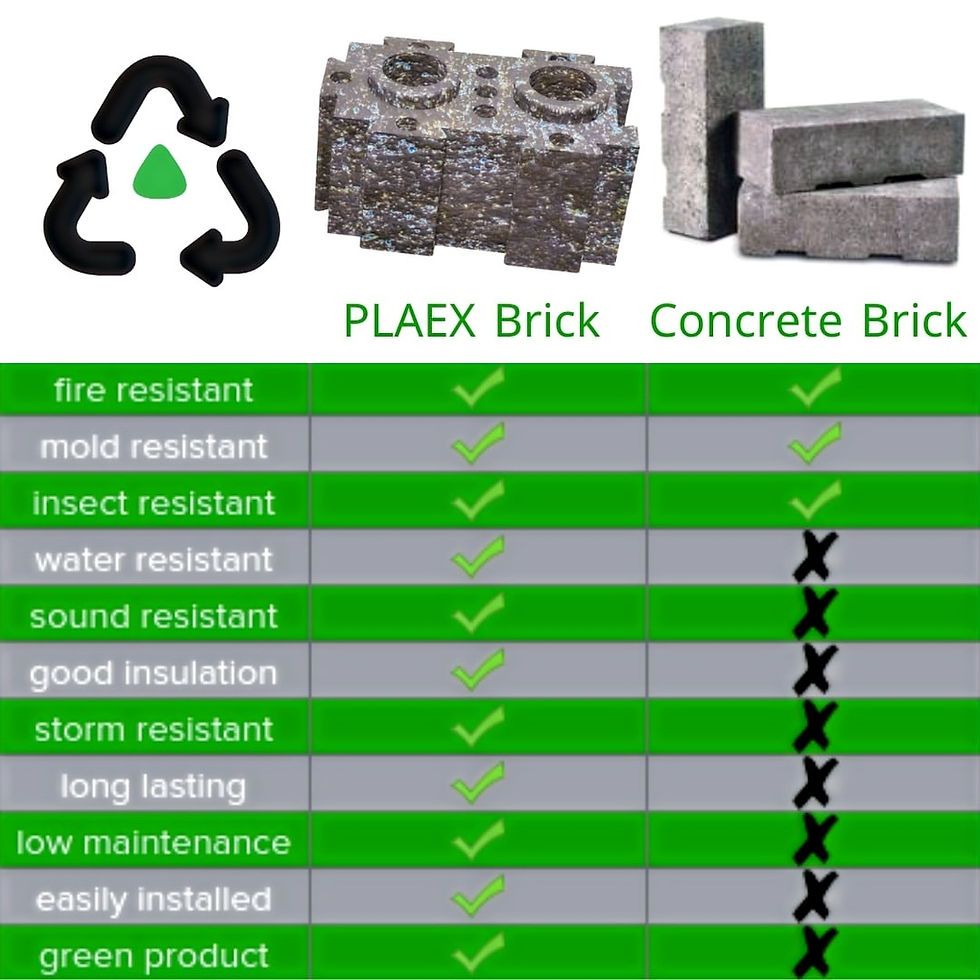
Credits to PLAEX
PLAEX: The new kid on the sustainable building block
PLAEX is making construction more sustainable and fun. But they’re not kidding.
Although being a young startup, PLAEX’s founder Dustin Bowers has been around the eco-block. He boasts over 18-year experience in the building industry, with hands-on expertise ranging from foundation to finish.
But when and how did the light bulb go off in the CEO’s head?
Back in 2017, Dustin was reading a research paper about using PL-astic as an A-ggregate into concrete mixture. And, of course, you need EX-trusion to get the final product.
And so PLAEX was born, or extruded if you like.
So, how does the process work?
Basically, they chuck the plastic waste into a funnel and shred it into small pieces. Then the plastic shred gets cleaned and mixed with other ingredients before going into an extruder. Once coming out the other end, you get a cement-like eco-paste with the bonus of being made of over 90% recycled materials.
What about the remaining 10%?
Colourants, UV & flame inhibitors will make up the rest.
While PLAEX can’t disclose the full technology yet, the company says their process is a closed-loop system requiring less steps compared to other recycling methods. And this means saving time, energy, and water.
How about the cost?
Initially, the bricks will be pegged at the same price as conventional systems. However, when you factor in faster prep and fewer production steps, PLAEX can deliver very low-cost sustainable building solutions.

Dustin Bowers, PLAEX's founder. Credits to PLAEX
The start-up is building momentum very fast.
After over funding their phase I, and successfully completing initial material testing with flying colours, they are now preparing to raise funds to launch a pilot plant in New Brunswick to start churning out their eco-friendly bricks.
The company strategically placed it nearby their raw materials sources (e.g., farms and marine industrial sites) to minimize their supply chain’s carbon footprint.
Phase II sets out on Nov 16th with the opening of their Seed round. The New Brunswick-based startup will also begin testing the resistance of their new sustainable building materials against earthquakes and other natural phenomena.
Also, more experiments will reveal other key parameters like R value (thermal resistance), energy efficiency and carbon footprint to compare their circular masterpiece with conventional building materials.
And the company is already looking further ahead, aiming to get their blocks approved by the Canadian Standards Association (CSA) in 2023.
For the time being, blocks may be used to build non-occupied structures like retaining walls, sheds and detached garages.
On top of that, the eco-blocks could be key in the environmental engineering field. As you can assemble them very quickly, they can turn into a last-minute protective barrier against flash floods and landslides.
However, PLAEX’s sustainable building materials might be also used for people’s homes in a few years.
Building a sustainable future one eco-brick at a time
PLAEX is the first off the blocks to come up with a Legolutionary smart and sustainable building system. This genius invention has already gone viral on YouTube.
If you’re an eco-builder who is after emission-breaking and zero-waste building materials, you should check out these eco-bricks.
They’re already going on the block, so make sure to order them now.
Commentaires